Hong Kong Geoguide 1: Guide to Retaining Wall Design (2020 Edition)
3 Construction Considerations in Design
3.3 Filter and Drainage Materials
3.3.1 Granular Filter and Drainage Materials
Free-draining granular materials such as clean crushed rock products are often used as filter and drainage materials. Such materials should be durable and free from clay, organic materials and other impurities. The grading of granular filter and drainage materials should conform to the filter design criteria given in Section 8.5. No-fines concrete should not be used as a filter material.
The particle size distributions of the retained insitu soil or backfill should be determined during the construction stage and checked against the relevant filter design criteria which should be stated on the drawings. Where the grading of the insitu soil is known at the design stage, the designer may, as an alternative, give the design grading envelopes for the filter and drainage materials on the drawings.
Compliance testing such as determination of grading and plasticity indices and compaction control testing such as insitu density and moisture content tests, together with acceptance criteria, should be specified. The frequency of such tests should take into account the likely variability of the various materials.
The level of compaction specified for filter and drainage materials should be compatible with the shear strength and permeability of these materials assumed in the design.
3.3.2 Geotextile Filter Materials
Where site conditions are non-aggressive, geotextile filters composed of resistant synthetic polymers are suitable as alternatives to granular filters in permanent works. Geotextile filters are relatively cheap and easy to use in construction. They are factory-produced materials and the control over geotextile properties is generally better than for a granular filter. Relevant criteria for geotextile filter design are given in Section 8.5.
It is recommended that only geotextiles produced by established international manufacturers should be used in permanent works. Polypropylene, polyester, polyamide and polyethylene, each with a molecular weight that exceeds 5 000, may be regarded as resistant synthetic polymers. Some general data on the chemical and thermal stability of synthetic polymer fibres is given in Table 5. In order to provide the geotextile fibres with resistance to deterioration caused by the effects of exposure and burial, the base polymer of the fibres should contain suitable additives such as UV stabilizers and anti-oxidants.
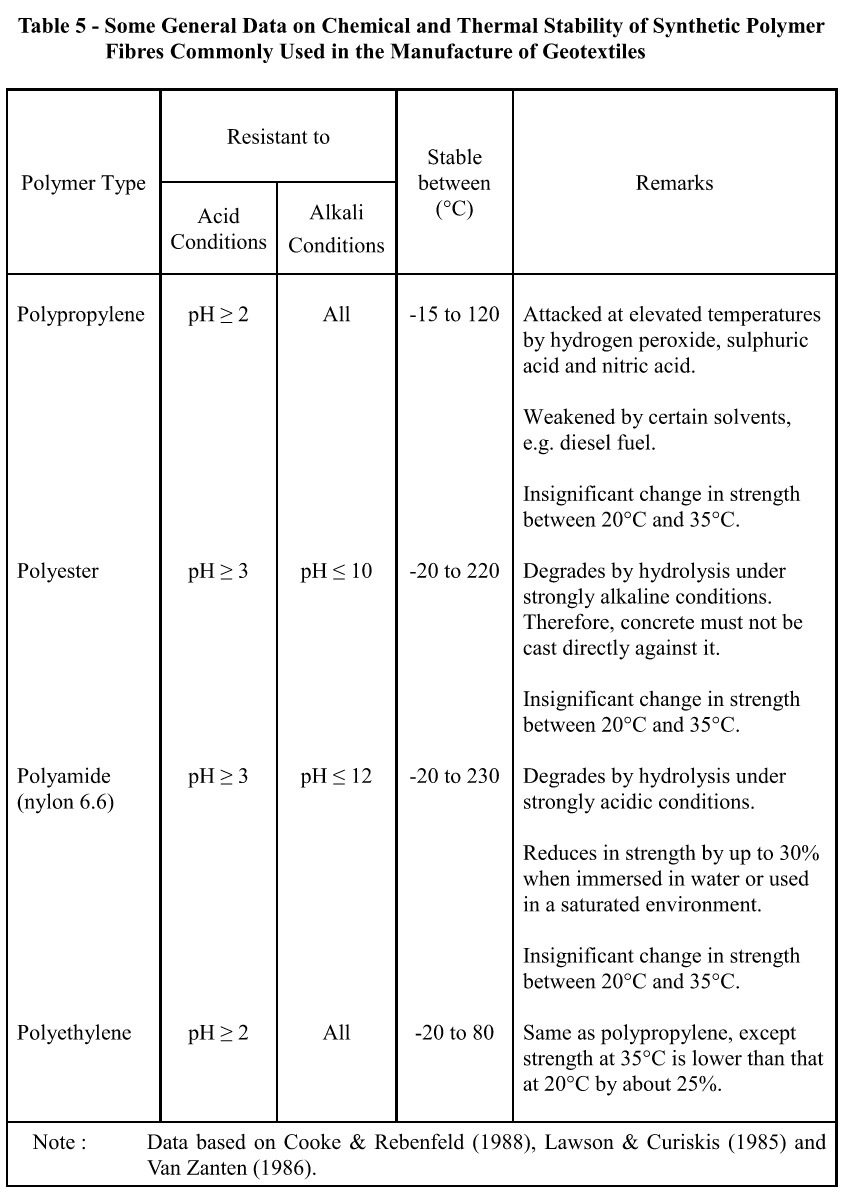
Where geotextile filters are intended to be used in permanent works, the site investigation should assess the potential aggressiveness of the site. As a minimum, the pH of the natural soil, the groundwater, and the fill to be placed close to the geotextile should be checked. Where aggressive conditions (e.g. pH outside the range of 5 to 10) are found to exist, advice should be sought from the geotextile manufacturer and, if necessary, polymer specialists. Particular care should also be taken where the site is in a potentially aggressive area, e.g. within a former industrial area or close to factories or waste disposal facilities.
Geotextiles in the ground may be damaged by vegetation roots and burrowing rodents. Although such damage is unlikely when a geotextile is buried at depth, it should be considered in the design when there is only a shallow soil cover.
To ensure that a geotextile filter will perform satisfactorily in service, it must have adequate hydraulic and mechanical properties, and the installation must be carried out in such a manner that the fabric is not damaged or excessively strained during construction. The level of supervision to be provided during installation should be appropriate to the risk category of the proposed works (GCO, 1984).
Geotextiles can deteriorate fairly rapidly under ultraviolet light. The effect of exposure is particularly important in Hong Kong where both solar radiation intensities and ambient temperatures are relatively high (Brand & Pang, 1991). Therefore, geotextile rolls delivered to a site should be maintained in roll form and covered (e.g. with opaque tubular sleeves) until they are to be installed. Geotextiles should be covered as soon as possible after installation. If it is foreseen that a geotextile cannot be protected within a short time after laying, allowance should be made in the design to ensure that a geotextile of adequate strength and ductility is specified for the period of exposure anticipated. Alternatively, the specification or drawings should state that geotextile strength and ductility requirements shall be met immediately prior to backfilling and that allowance shall be made in the provision of geotextiles for any deterioration in properties due to exposure. Tensile testing of geotextile samples taken immediately prior to covering may be carried out to ensure that the geotextile installed meets the specified quality. The acceptance criterion for the tensile testing should take into account the variability of the materials.
Drainage materials placed adjacent to a geotextile filter should preferably not contain particles larger than 75 mm. If drainage aggregates of a relatively uniform size are used, the maximum size of the particles should be limited to 20 mm in order to minimize the 'span' of the geotextile across the particles.
It is important to ensure that the geotextile filter is installed in good contact with the adjacent soil. Additional guidance on the installation of geotextiles can be found in GEO Publication No. 1/93 (GEO, 1993).
Where appropriate, earth pressure calculations should consider the effect of a reduced shear strength at interfaces between soil and geotextile. In cases where the interface strength is likely to be a critical factor in a design, direct shear tests should be carried out to determine the interface shear strength. Alternatively, the shearing resistance can be improved by benching the insitu ground on which the geotextile is to be placed.
3.4 Construction Method and Sequence
Selection of the method and sequence of construction is usually undertaken by the contractor. However, there may be instances where a particular method or sequence of operations is dictated by the design. In such cases, it is necessary to check that the method and consequence of operations are not intrinsically risky. In other instances, the designer may wish or be required to stipulate the methods of construction. In all cases, there should be suitable controls, e.g. by requiring the submission of method statements, so that an assessment can be made during construction (see Chapter 12).
The tolerances of the completed wall should be specified and these should take account of possible construction methods, as well as any movements which may occur during construction (e.g. due to settlement of the foundation). The processes of excavation, filling, pumping, etc. should be so arranged as to avoid endangering the stability and reducing the strength of any portion of the retaining wall, including any partially-completed sections. For example, in the case of a retaining wall designed to be supported at the top, backfilling should not proceed until the support is provided. Alternatively, the wall should be designed for the partially-completed loading condition. Limits of permissible loadings (e.g. surcharge) on the retaining wall should be clearly stated on the drawings.
|